シリコンカーバイド入門
炭化ケイ素(SiC)は、炭素とシリコンからなる複合半導体材料であり、高温、高周波、高出力、高電圧デバイスの製造に理想的な材料の1つです。従来のシリコン材料(Si)と比較して、炭化ケイ素のバンドギャップはシリコンの3倍です。熱伝導率はシリコンの4〜5倍です。破壊電圧はシリコンの8〜10倍です。電子飽和ドリフト率はシリコンの2〜3倍であり、現代産業の高出力、高電圧、高周波のニーズを満たしています。主に高速、高周波、高出力、発光電子部品の製造に使用されます。下流の応用分野には、スマートグリッド、新エネルギー車、太陽光発電、風力発電、5G通信などがあります。炭化ケイ素ダイオードとMOSFETはすでに商業化されています。
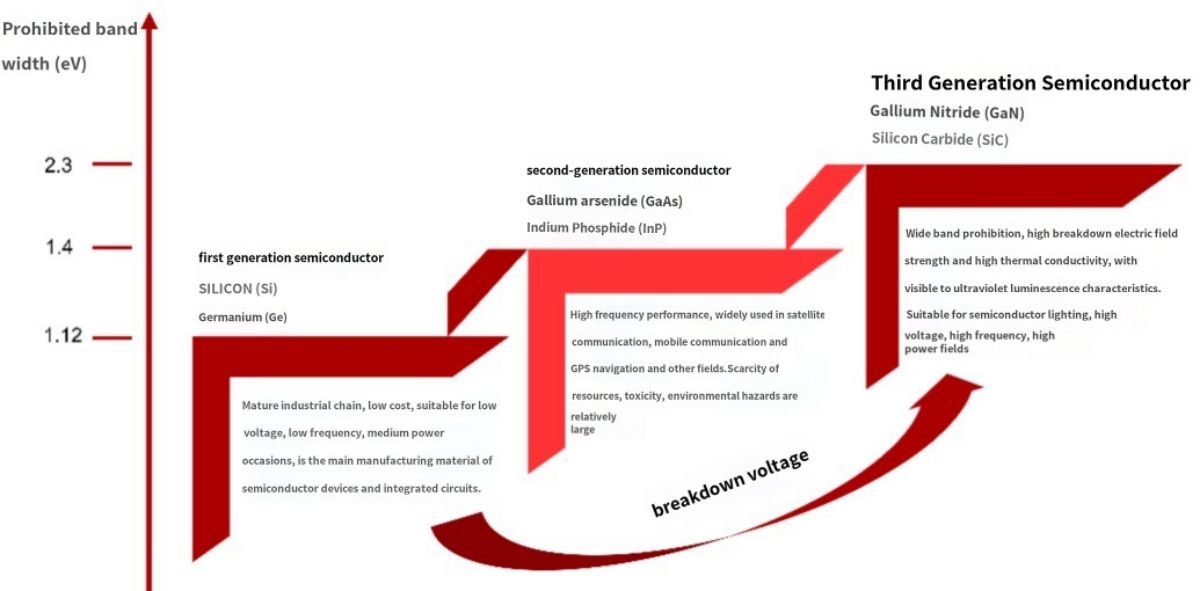
耐高温性。炭化ケイ素のバンドギャップ幅はシリコンの2~3倍で、高温下でも電子が遷移しにくく、より高い動作温度に耐えることができます。また、炭化ケイ素の熱伝導率はシリコンの4~5倍であるため、デバイスの放熱が容易になり、動作限界温度が高くなります。この耐高温性により、電力密度が大幅に向上するとともに、冷却システムへの要求が軽減され、端末の軽量化と小型化が実現します。
高圧に耐えます。シリコンカーバイドの破壊電界強度はシリコンの10倍で、より高い電圧に耐えることができ、高電圧デバイスに適しています。
高周波耐性。炭化ケイ素はシリコンの2倍の飽和電子ドリフト速度を持ち、シャットダウンプロセス中の電流テーリングがないため、デバイスのスイッチング周波数を効果的に向上させ、デバイスの小型化を実現します。
低エネルギー損失。シリコンカーバイドはシリコン材料と比較して、オン抵抗とオン損失が非常に低いという特徴があります。同時に、シリコンカーバイドの広いバンドギャップ幅は、リーク電流と電力損失を大幅に低減します。さらに、シリコンカーバイドデバイスはシャットダウン時に電流の引きずり現象がなく、スイッチング損失も低く抑えられます。
シリコンカーバイド産業チェーン
主に基板、エピタキシー、デバイス設計、製造、封止などが含まれます。シリコンカーバイドは、材料から半導体パワーデバイスに至るまで、単結晶成長、インゴットのスライス、エピタキシャル成長、ウェーハ設計、製造、パッケージングなどのプロセスを経ます。シリコンカーバイド粉末の合成後、まずシリコンカーバイドインゴットを製造し、スライス、研削、研磨によってシリコンカーバイド基板を得、エピタキシャル成長によってエピタキシャルシートを得ます。エピタキシャルウェーハは、リソグラフィー、エッチング、イオン注入、金属パッシベーションなどのプロセスを経てシリコンカーバイドから製造され、ウェーハはダイに切断され、デバイスはパッケージングされ、デバイスは専用のシェルに結合され、モジュールに組み立てられます。
産業チェーンの上流1:基板 - 結晶成長はコアプロセスリンクです
シリコンカーバイド基板は、シリコンカーバイドデバイスのコストの約47%を占め、製造技術障壁が最も高く、価値も最も高く、将来のSiC大規模産業化の中核です。
電気化学特性の違いから、シリコンカーバイド基板材料は導電性基板(抵抗率15~30mΩ·cm)と半絶縁性基板(抵抗率105Ω·cm以上)に分けられます。これらの2種類の基板は、エピタキシャル成長後にそれぞれパワーデバイスや高周波デバイスなどの個別デバイスの製造に使用されます。このうち、半絶縁性シリコンカーバイド基板は、主に窒化ガリウムRFデバイスや光電デバイスなどの製造に使用されます。半絶縁性SiC基板上にGaNエピタキシャル層を成長させることでSiCエピタキシャル基板が作製され、これをさらにHEMT(窒化ガリウムRFデバイス)に加工することができます。導電性シリコンカーバイド基板は、主にパワーデバイスの製造に使用されます。従来のシリコンパワーデバイス製造プロセスとは異なり、シリコンカーバイドパワーデバイスはシリコンカーバイド基板上に直接製造することができず、導電性基板上にシリコンカーバイドエピタキシャル層を成長させてシリコンカーバイドエピタキシャルシートを得る必要があり、エピタキシャル層はショットキーダイオード、MOSFET、IGBTなどのパワーデバイス上に製造されます。
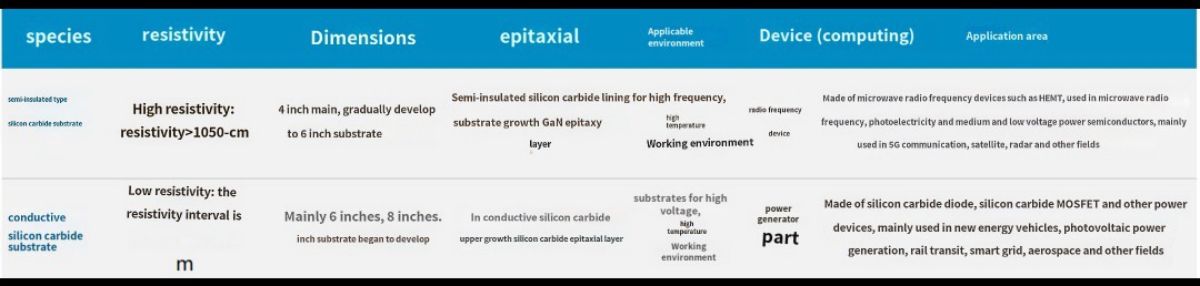
高純度炭素粉末と高純度シリコン粉末から炭化ケイ素粉末を合成し、特殊な温度場下で様々なサイズの炭化ケイ素インゴットを育成した後、複数の加工プロセスを経て炭化ケイ素基板を製造しました。コアプロセスは以下のとおりです。
原料合成:高純度シリコン粉末とトナーを配合に従って混合し、反応室で2000℃以上の高温条件下で反応させることで、特定の結晶型と粒子サイズを持つ炭化ケイ素粒子を合成します。その後、粉砕、ふるい分け、洗浄などの工程を経て、高純度シリコン炭化ケイ素粉末原料の要件を満たします。
結晶成長はシリコンカーバイド基板製造の中核プロセスであり、シリコンカーバイド基板の電気的特性を決定づける。現在、結晶成長の主な方法は、物理気相成長法(PVT法)、高温化学気相成長法(HT-CVD法)、液相エピタキシー法(LPE法)である。その中でも、PVT法は技術的成熟度が最も高く、エンジニアリング分野で最も広く利用されている、現在商業的なSiC基板成長の主流となっている。
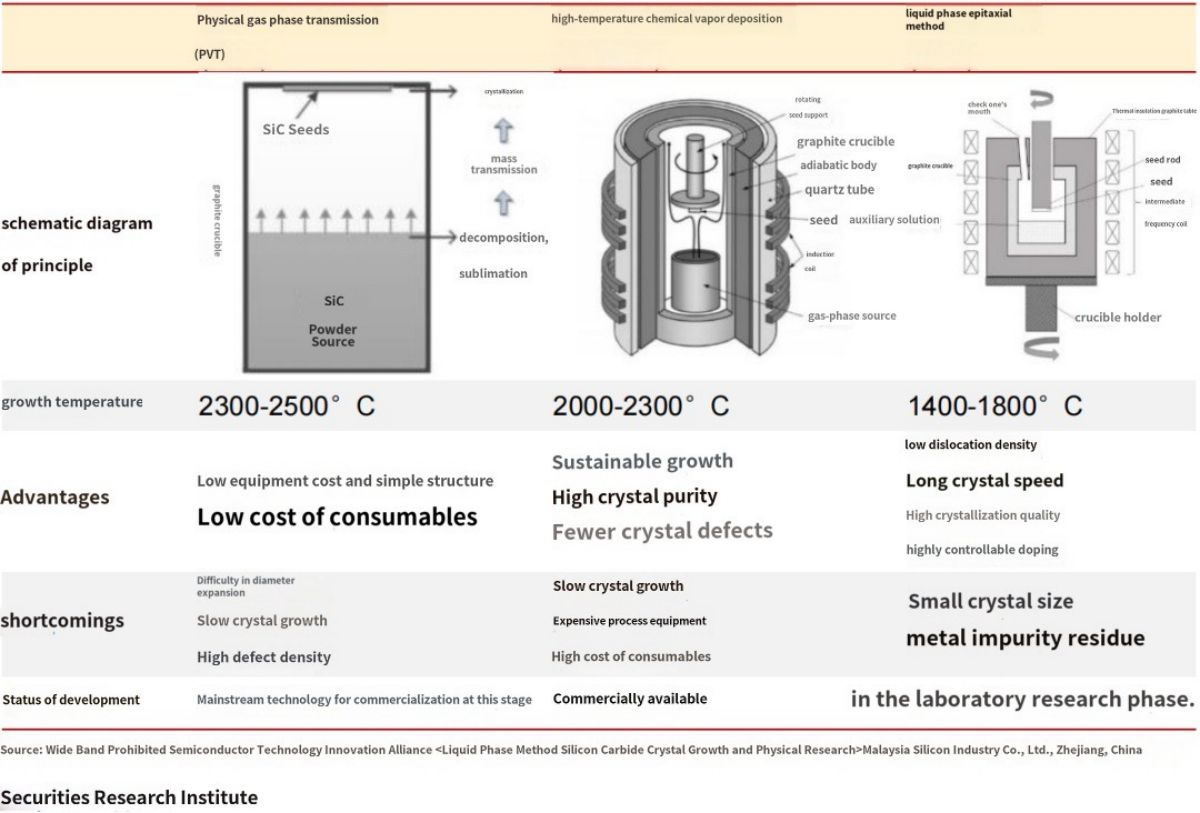
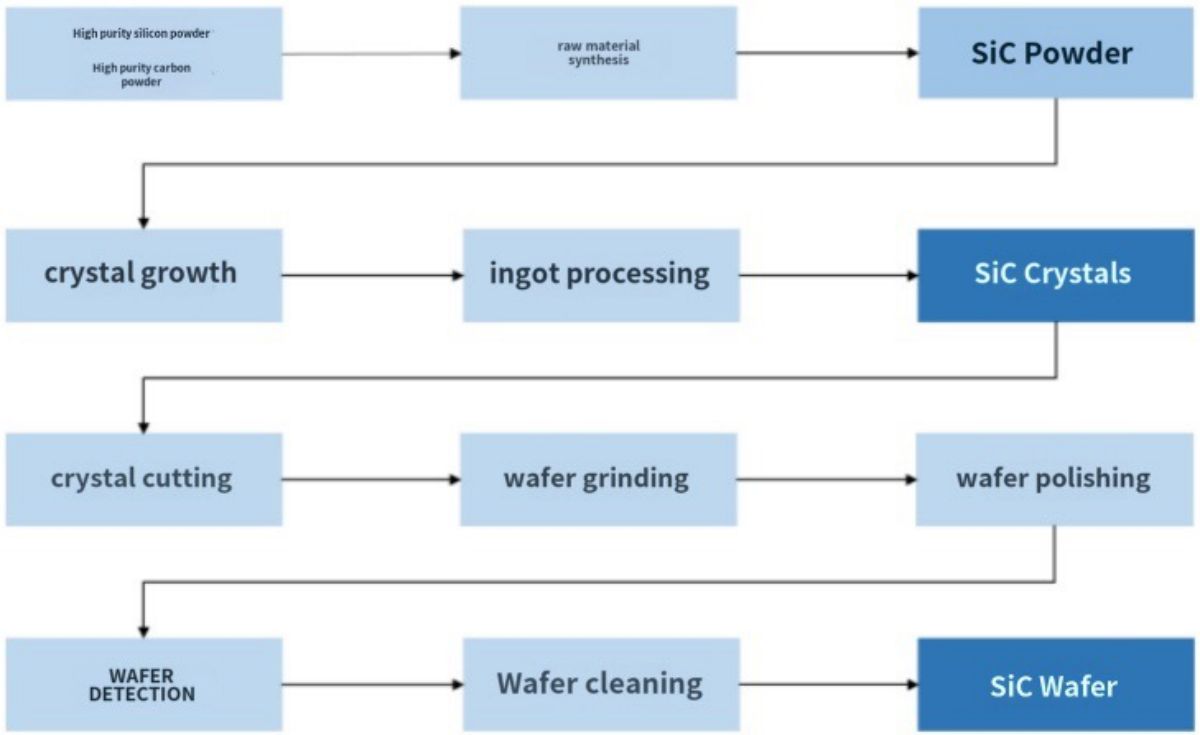
SiC基板の製造は難しく、価格が高くなる。
温度場制御は難しい:Si結晶棒の成長は1500℃で済むのに対し、SiC結晶棒は2000℃以上の高温で成長させる必要があり、SiC異性体は250種類以上ありますが、パワーデバイスの製造に主に用いられる4H-SiC単結晶構造は、精密に制御しないと他の結晶構造になってしまいます。また、るつぼ内の温度勾配は、SiC昇華転写速度や結晶界面における気体原子の配列と成長モードを決定し、結晶成長速度と結晶品質に影響を与えるため、体系的な温度場制御技術を形成する必要があります。Si材料と比較して、SiC製造における違いは、高温イオン注入、高温酸化、高温活性化などの高温プロセスと、これらの高温プロセスに必要なハードマスクプロセスにもあります。
結晶成長が遅い:Si結晶棒の成長速度は30〜150mm/hに達し、1〜3mのシリコン結晶棒の生産には約1日しかかかりません。PVT法によるSiC結晶棒を例にとると、成長速度は約0.2〜0.4mm/hで、7日間で3〜6cm未満しか成長せず、成長率はシリコン材料の1%未満であり、生産能力は非常に限られています。
製品パラメータが高く、歩留まりが低い:SiC基板のコアパラメータには、微小管密度、転位密度、抵抗率、反り、表面粗さなどが含まれます。パラメータ指標を制御しながら、高温密閉チャンバー内で原子を配置し、結晶成長を完了するのは、複雑なシステムエンジニアリングです。
この材料は硬度が高く、脆性が高く、切削時間が長く、摩耗も大きいという欠点があります。SiCのモース硬度は9.25でダイヤモンドに次ぐ硬さであり、切断、研削、研磨の難易度が著しく高まります。厚さ3cmのインゴットを35~40個切断するには約120時間を要します。また、SiCは脆性が高いため、ウェーハ加工時の摩耗が大きく、生産性は60%程度にとどまります。
開発動向:大型化+価格低下
世界のSiC市場では6インチ量産ラインが成熟し、大手企業が8インチ市場に参入しています。国内の開発プロジェクトは主に6インチです。現在、国内企業の多くはまだ4インチ生産ラインをベースとしていますが、業界は徐々に6インチへと拡大しており、6インチ対応設備技術の成熟に伴い、国内のSiC基板技術も徐々に向上しています。大型生産ラインの規模の経済性が反映され、現在の国内6インチ量産までの時間差は7年に縮まっています。ウェーハサイズが大きいほど、単一チップ数が増加し、歩留まりが向上し、エッジチップの割合が減り、研究開発費と歩留まり損失が約7%に抑えられ、ウェーハ利用率が向上します。
デバイスの設計にはまだ多くの困難がある
SiCダイオードの実用化は徐々に進んでおり、現在、多くの中国メーカーがSiC SBD製品を設計しています。中電圧・高電圧SiC SBD製品は優れた安定性を備えており、車載OBCではSiC SBD+SI IGBTの組み合わせにより安定した電流密度を実現しています。現在、中国におけるSiC SBD製品の特許設計には障壁がなく、海外との差も小さいです。
SiC MOSは依然として多くの課題を抱えており、SiC MOSと海外メーカーの間には依然として大きな隔たりがあり、関連する製造プラットフォームも構築段階にあります。現在、ST、Infineon、Rohmなどの600~1700V SiC MOSは量産体制を整え、多くの製造業と契約・出荷を締結しています。一方、国内のSiC MOS設計は既にほぼ完了しており、多くの設計メーカーがウェハフロー段階でファブと連携して作業を進めています。その後の顧客検証にはまだ時間を要するため、大規模な商用化にはまだ長い道のりが残されています。
現在、平面構造が主流であり、将来的にはトレンチ型が高圧分野で広く採用されるでしょう。平面構造のSiC MOSメーカーは多く、平面構造は溝型に比べて局所的な破壊が生じにくく、動作安定性に影響を与えにくいため、1200V以下の市場では幅広い応用価値を有しています。また、平面構造は製造工程が比較的単純であるため、製造性とコスト管理という2つの側面を満たすことができます。溝型デバイスは、寄生インダクタンスが極めて低く、スイッチング速度が速く、損失が少なく、比較的高性能であるという利点があります。
2--SiCウエハニュース
炭化ケイ素市場の生産と販売の成長、需給構造の不均衡に注意
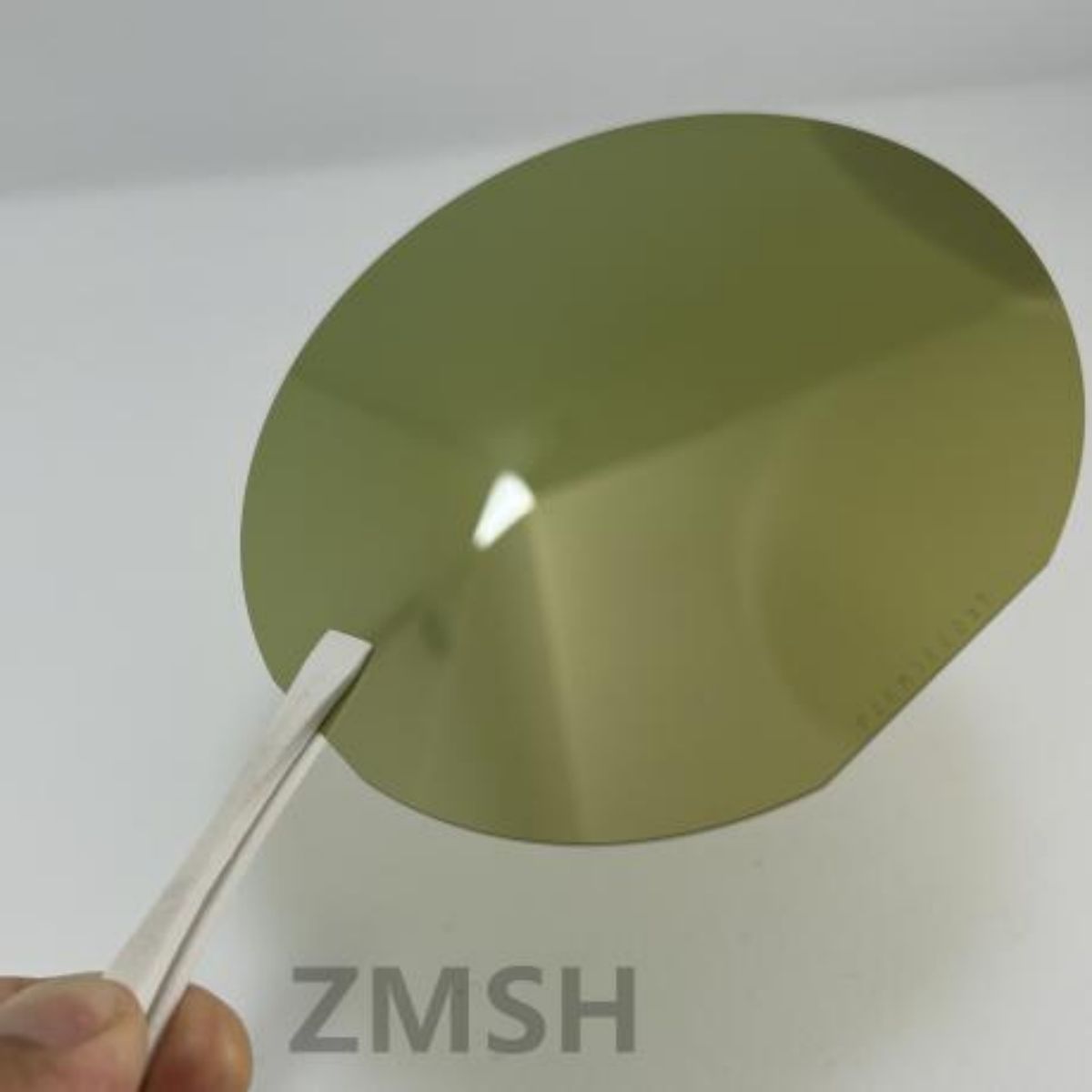
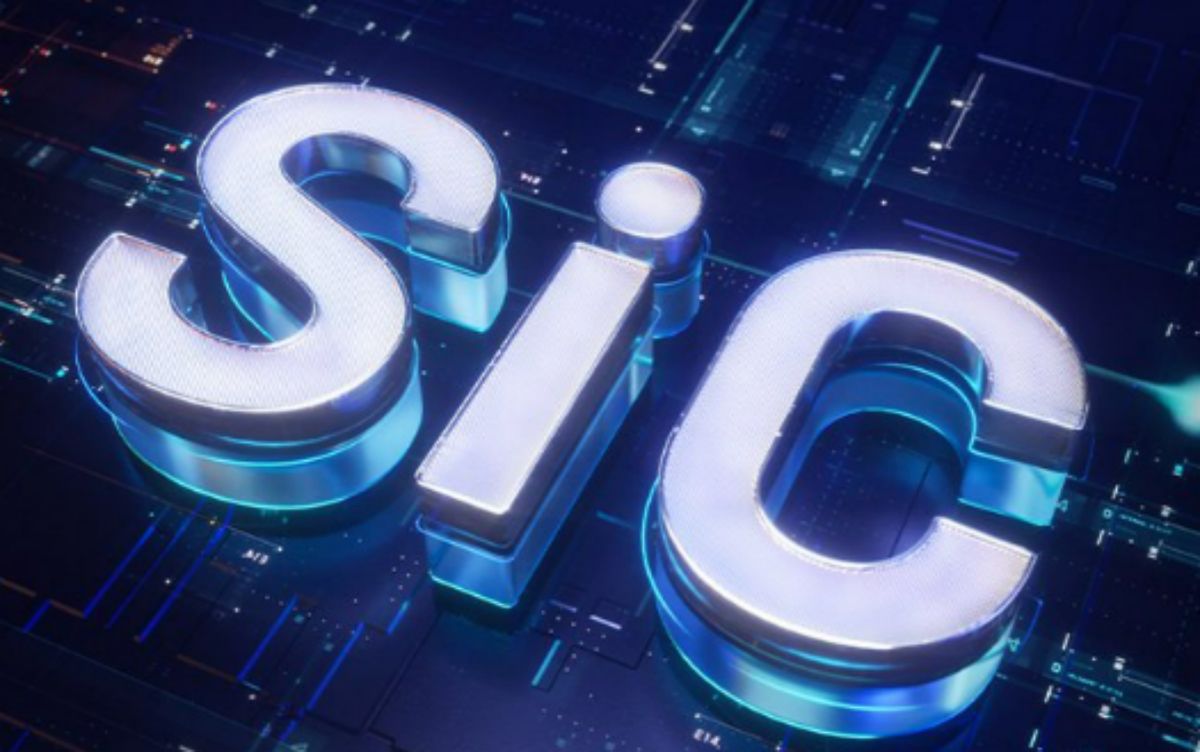
高周波・高出力パワーエレクトロニクスの市場需要の急速な成長に伴い、シリコンベースの半導体デバイスの物理的限界ボトルネックが徐々に顕著になり、炭化ケイ素(SiC)に代表される第三世代半導体材料が徐々に産業化されました。材料性能の観点から見ると、炭化ケイ素はシリコン材料の3倍のバンドギャップ幅、10倍の臨界破壊電界強度、3倍の熱伝導率を備えているため、炭化ケイ素パワーデバイスは高周波、高圧、高温などの用途に適しており、パワーエレクトロニクスシステムの効率と電力密度の向上に役立ちます。
現在、SiCダイオードとSiC MOSFETは徐々に市場に投入され、より成熟した製品もあります。その中で、SiCダイオードは、逆回復電荷の利点がないため、一部の分野でシリコンベースのダイオードの代わりに広く使用されています。SiC MOSFETも、自動車、エネルギー貯蔵、充電パイル、太陽光発電などの分野で徐々に使用されています。自動車アプリケーションの分野では、モジュール化の傾向がますます顕著になり、SiCの優れた性能を実現するには、高度なパッケージングプロセスに依存する必要があります。技術的には、比較的成熟したシェルシーリングが主流であり、将来的には、プラスチックシーリングの開発、そのカスタマイズされた開発特性は、SiCモジュールにより適しています。
シリコンカーバイド価格下落のスピードは想像を超える
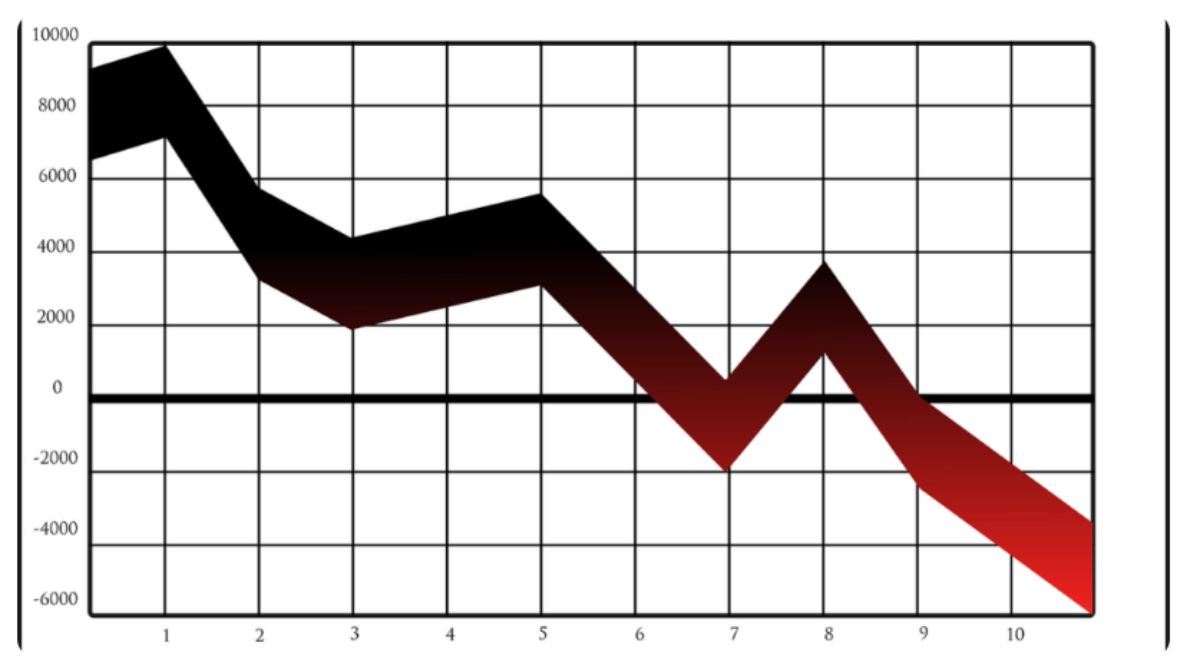
シリコンカーバイドデバイスの応用は、主に高コストによって制限されています。同レベルのSiC MOSFETの価格は、SiベースのIGBTの4倍にも達します。これは、シリコンカーバイドのプロセスが複雑で、単結晶およびエピタキシャル成長が環境に厳しいだけでなく、成長速度が遅く、単結晶を基板に加工する際に切断・研磨工程を経なければならないためです。その材料特性と未成熟な加工技術により、国産基板の歩留まりは50%未満であり、さまざまな要因が基板およびエピタキシャル価格の高騰につながっています。
しかし、シリコンカーバイドデバイスとシリコンベースデバイスのコスト構成は正反対で、フロントチャネルの基板コストとエピタキシャルコストはそれぞれデバイス全体の47%と23%を占め、合計で約70%を占めています。一方、バックチャネルのデバイス設計、製造、シーリングリンクはわずか30%を占めています。シリコンベースデバイスの生産コストは主にバックチャネルのウェハ製造に集中しており、約50%を占めています。基板コストはわずか7%です。シリコンカーバイド産業チェーンの価値が逆転している現象は、上流の基板エピタキシャルメーカーが中核的な発言権を握っていることを意味し、これが国内外の企業の配置の鍵となります。
市場の動態的視点から見ると、シリコンカーバイドのコスト削減は、シリコンカーバイドの長結晶化とスライス工程の改善に加え、ウェハサイズの拡大にもつながります。これは、半導体開発における過去の成熟路線でもあります。Wolfspeedのデータによると、シリコンカーバイド基板を6インチから8インチにアップグレードすることで、良質なチップの生産量が80%~90%増加し、歩留まりの向上にも貢献します。これにより、複合単価は50%削減されます。
2023年は「8インチSiC元年」と呼ばれ、今年、国内外のシリコンカーバイドメーカーは8インチシリコンカーバイドの配置を加速させています。例えば、Wolfspeedはシリコンカーバイドの生産拡大に145.5億ドルを投じ、その重要な部分は8インチSiC基板製造工場の建設であり、将来的に多くの企業に200mm SiCベアメタルの供給を確保するためです。国内のTianyue AdvancedとTianke Hedaも、将来的に8インチシリコンカーバイド基板を供給するためにInfineonと長期契約を締結しました。
今年からシリコンカーバイドは6インチから8インチへと加速し、Wolfspeedは2024年までに8インチ基板のチップ単位コストが2022年の6インチ基板のチップ単位コストと比較して60%以上削減されると予想しており、コスト低下によりアプリケーション市場がさらに開拓されるとJi Bond Consultingの調査データは指摘しています。現在の8インチ製品の市場シェアは2%未満ですが、2026年までに市場シェアは約15%に成長すると予想されています。
実際、シリコンカーバイド基板の価格下落率は多くの人の想像を超えており、現在市場で6インチ基板の供給は1枚あたり4000~5000元で、年初と比べて大幅に下落し、来年は4000元を下回ると予想されています。注目すべきは、一部のメーカーが最初の市場を獲得するために、販売価格をコストライン以下に引き下げ、価格競争のモデルを開き、主に低電圧分野のシリコンカーバイド基板の供給が比較的十分であることに集中しているため、国内外のメーカーが積極的に生産能力を拡大し、あるいはシリコンカーバイド基板が想像よりも早く供給過剰の段階に至らせているということです。
投稿日時: 2024年1月19日