ウェットクリーニング(ウェットクリーン)は半導体製造プロセスにおける重要なステップの 1 つであり、ウェーハの表面からさまざまな汚染物質を除去して、後続のプロセスステップをクリーンな表面で実行できるようにすることを目的としています。
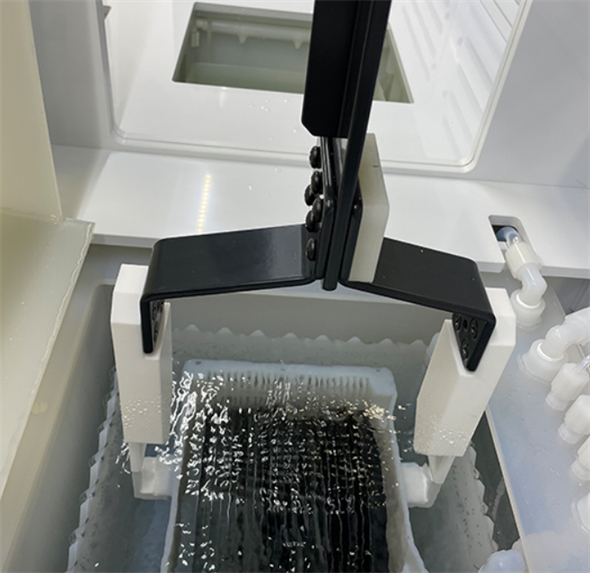
半導体デバイスの小型化と高精度化が進むにつれ、ウェーハ洗浄プロセスに対する技術的要求はますます厳しくなっています。ウェーハ表面に付着したごく微細な粒子、有機物、金属イオン、酸化物残留物でさえ、デバイス性能に重大な影響を与え、半導体デバイスの歩留まりと信頼性に悪影響を及ぼす可能性があります。
ウェーハ洗浄の基本原則
ウェーハ洗浄の核心は、物理的、化学的、およびその他の方法によってウェーハ表面からさまざまな汚染物質を効果的に除去し、後続の処理に適したクリーンな表面をウェーハに確保することにあります。
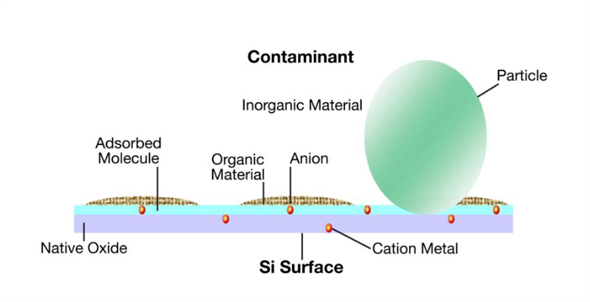
汚染の種類
デバイス特性への主な影響
記事の汚染 | パターン欠陥
イオン注入欠陥
絶縁膜破壊欠陥
| |
金属汚染 | アルカリ金属 | MOSトランジスタの不安定性
ゲート酸化膜の破壊/劣化
|
重金属 | PN接合逆リーク電流の増加
ゲート酸化膜破壊欠陥
少数キャリアの寿命低下
酸化物励起層欠陥生成
| |
化学物質汚染 | 有機材料 | ゲート酸化膜破壊欠陥
CVDフィルムの変動(インキュベーション時間)
熱酸化膜の厚さの変化(加速酸化)
ヘイズ発生(ウェーハ、レンズ、ミラー、マスク、レチクル)
|
無機ドーパント(B、P) | MOSトランジスタのVthシフト
Si基板と高抵抗ポリシリコンのシート抵抗の変動
| |
無機塩基(アミン、アンモニア)と酸(SOx) | 化学増幅レジストの解像度の低下
塩分生成による粒子汚染とヘイズの発生
| |
湿気、空気による自然酸化膜と化学酸化膜 | 接触抵抗の増加
ゲート酸化膜の破壊/劣化
|
具体的には、ウェーハ洗浄プロセスの目的は次のとおりです。
パーティクル除去:物理的または化学的な方法を用いて、ウェーハ表面に付着した小さなパーティクルを除去します。小さなパーティクルは、ウェーハ表面との間に強い静電力が生じるため除去が困難であり、特別な処理が必要となります。
有機物除去:グリースやフォトレジスト残渣などの有機汚染物質がウェーハ表面に付着することがあります。これらの汚染物質は通常、強力な酸化剤や溶剤を用いて除去されます。
金属イオン除去:ウェーハ表面に残留する金属イオンは、電気特性を劣化させ、後続の処理工程に影響を及ぼす可能性があります。そのため、これらのイオンを除去するために、特殊な化学溶液が使用されます。
酸化物除去:一部のプロセスでは、ウェーハ表面にシリコン酸化物などの酸化物層がないことが求められます。このような場合、特定の洗浄工程で自然酸化物層を除去する必要があります。
ウェーハ洗浄技術の課題は、表面の荒れ、腐食、その他の物理的損傷を防ぐなど、ウェーハ表面に悪影響を与えることなく、汚染物質を効率的に除去することです。
2. ウェーハ洗浄プロセスフロー
ウェーハ洗浄プロセスには通常、汚染物質を完全に除去し、完全にきれいな表面を実現するために複数のステップが含まれます。
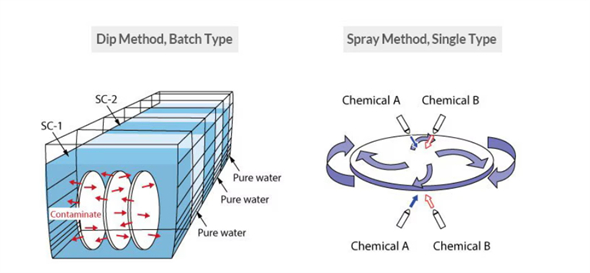
図:バッチ式洗浄と枚葉式洗浄の比較
一般的なウェーハ洗浄プロセスには、次の主な手順が含まれます。
1. プレクリーニング(プレクリーン)
前洗浄の目的は、ウェーハ表面から遊離汚染物質や大きな粒子を除去することです。これは通常、脱イオン水(DI Water)リンスと超音波洗浄によって実現されます。脱イオン水はウェーハ表面から粒子や溶解不純物を最初に除去し、超音波洗浄はキャビテーション効果を利用して粒子とウェーハ表面の結合を切断し、粒子の除去を容易にします。
2. 化学洗浄
化学洗浄はウェーハ洗浄プロセスの中核となるステップの 1 つであり、化学溶液を使用してウェーハ表面から有機物、金属イオン、酸化物を除去します。
有機物除去:有機汚染物質の溶解と酸化には、通常、アセトンまたはアンモニア/過酸化水素混合液(SC-1)が使用されます。SC-1溶液の典型的な比率は、NH₄OHです。
₂O₂
₂O = 1:1:5、動作温度は約20°Cです。
金属イオン除去:ウェーハ表面から金属イオンを除去するには、硝酸または塩酸/過酸化水素混合液(SC-2)を使用します。SC-2溶液の典型的な比率は、HClです。
₂O₂
₂O = 1:1:6、温度は約80℃に維持されます。
酸化膜除去:一部のプロセスでは、ウェーハ表面の自然酸化膜の除去が必要であり、そのためにフッ化水素酸(HF)溶液が使用されます。HF溶液の典型的な比率はHF
₂O=1:50で常温でも使用可能です。
3. 最終清掃
化学洗浄後、ウェーハは通常、表面に化学残留物が残らないように最終洗浄工程を経ます。最終洗浄では、主に脱イオン水を用いて徹底的にすすぎます。さらに、オゾン水洗浄(O₃/H₂O)を用いて、ウェーハ表面に残留する汚染物質をさらに除去します。
4. 乾燥
洗浄されたウェーハは、ウォーターマークや汚染物質の再付着を防ぐために、迅速に乾燥させる必要があります。一般的な乾燥方法には、スピン乾燥と窒素パージがあります。前者はウェーハを高速回転させることにより表面から水分を除去し、後者は乾燥窒素ガスをウェーハ表面に吹き付けることで完全な乾燥を実現します。
汚染物質
清掃手順名
化学混合物の説明
化学薬品
粒子 | ピラニア(SPM) | 硫酸/過酸化水素/純水 | H2SO4/H2O2/H2O 3-4:1; 90°C |
SC-1(APM) | 水酸化アンモニウム/過酸化水素/脱イオン水 | NH4OH/H2O2/H2O 1:4:20; 80°C | |
金属(銅以外) | SC-2(HPM) | 塩酸/過酸化水素/脱イオン水 | HCl/H2O2/H2O1:1:6; 85°C |
ピラニア(SPM) | 硫酸/過酸化水素/純水 | H2SO4/H2O2/H2O3-4:1; 90°C | |
DHF | 希フッ化水素酸/DI水(銅は除去しません) | HF/H2O1:50 | |
オーガニック | ピラニア(SPM) | 硫酸/過酸化水素/純水 | H2SO4/H2O2/H2O 3-4:1; 90°C |
SC-1(APM) | 水酸化アンモニウム/過酸化水素/脱イオン水 | NH4OH/H2O2/H2O 1:4:20; 80°C | |
DIO3 | 脱イオン水中のオゾン | O3/H2O最適化混合物 | |
自然酸化物 | DHF | 希フッ化水素酸/脱イオン水 | HF/H2O 1:100 |
BHF | 緩衝フッ化水素酸 | NH4F/HF/H2O |
3. 一般的なウェーハ洗浄方法
1. RCAクリーニング方法
RCA洗浄法は、半導体業界で最も古典的なウェーハ洗浄技術の一つであり、RCAコーポレーションによって40年以上前に開発されました。この方法は主に有機汚染物質と金属イオン不純物の除去に使用され、SC-1(標準洗浄1)とSC-2(標準洗浄2)の2つのステップで完了します。
SC-1洗浄:この工程は主に有機汚染物質やパーティクルを除去するために使用されます。溶液はアンモニア、過酸化水素、水の混合液で、ウェーハ表面に薄いシリコン酸化物層を形成します。
SC-2洗浄:この工程は主に金属イオン汚染物質を除去するために行われ、塩酸、過酸化水素、水の混合液を使用します。ウェーハ表面に薄い不活性化層を形成し、再汚染を防ぎます。
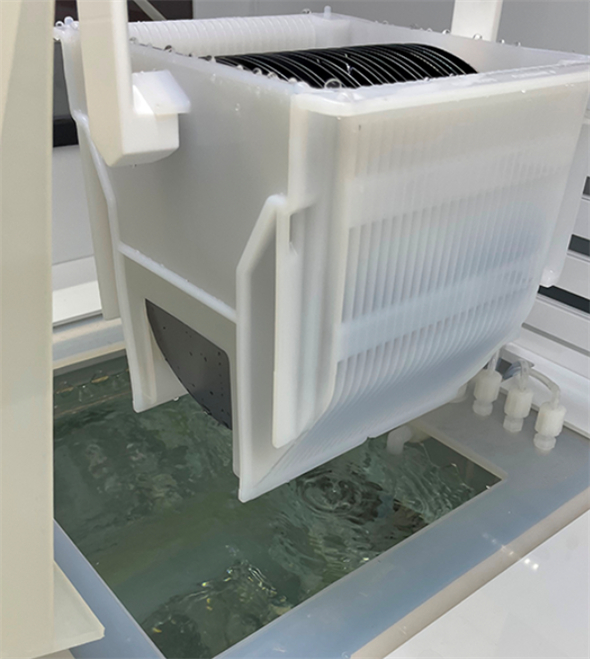
2. ピラニア洗浄法(ピラニアエッチクリーン)
ピラニア洗浄法は、硫酸と過酸化水素の混合液(通常は3:1または4:1の比率)を用いて有機物を除去する非常に効果的な手法です。この溶液は非常に強力な酸化力を持つため、大量の有機物や頑固な汚染物質を除去できます。この方法では、ウェハへのダメージを避けるため、特に温度と濃度に関して、条件を厳密に管理する必要があります。
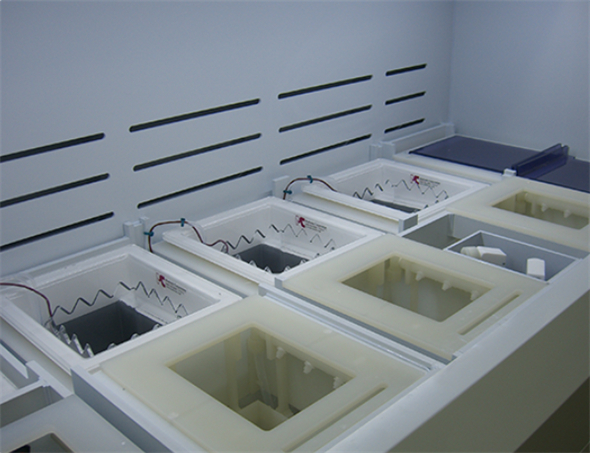
超音波洗浄は、液体中の高周波音波によって発生するキャビテーション効果を利用して、ウェーハ表面から汚染物質を除去します。従来の超音波洗浄と比較して、メガソニック洗浄はより高い周波数で動作するため、ウェーハ表面に損傷を与えることなく、サブミクロンサイズの粒子をより効率的に除去できます。
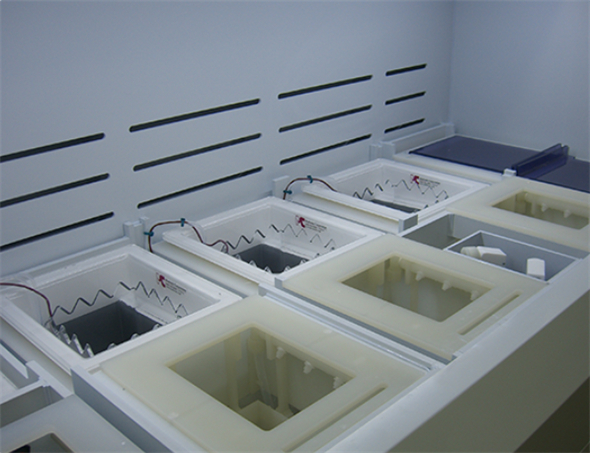
4. オゾン洗浄
オゾン洗浄技術は、オゾンの強力な酸化作用を利用してウェーハ表面の有機汚染物質を分解・除去し、最終的に無害な二酸化炭素と水に変換します。この方法は高価な化学試薬を必要とせず、環境汚染も少ないため、ウェーハ洗浄分野における新興技術となっています。
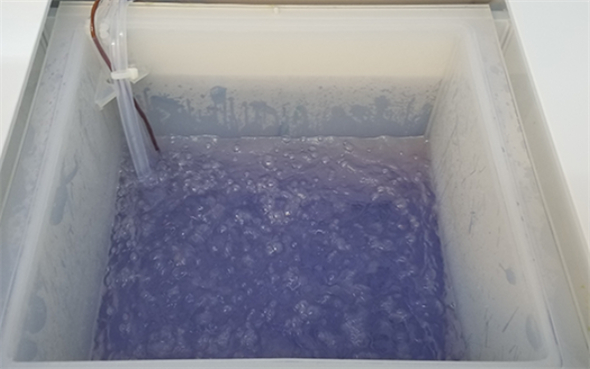
4. ウェーハ洗浄プロセス装置
半導体製造においては、ウェーハ洗浄プロセスの効率性と安全性を確保するため、様々な高度な洗浄装置が使用されています。主な種類は以下の通りです。
1. ウェットクリーニング機器
ウェット洗浄装置には、様々な浸漬タンク、超音波洗浄タンク、スピンドライヤーが含まれます。これらの装置は、機械的な力と化学試薬を組み合わせて、ウェーハ表面から汚染物質を除去します。浸漬タンクには通常、化学溶液の安定性と効果を確保するための温度制御システムが装備されています。
2. ドライクリーニング機器
ドライクリーニング装置には主にプラズマクリーナーが含まれます。プラズマクリーナーは、プラズマ中の高エネルギー粒子を用いてウェーハ表面の残留物と反応し、残留物を除去します。プラズマクリーニングは、化学残留物を発生させることなく表面の完全性を維持する必要があるプロセスに特に適しています。
3. 自動清掃システム
半導体生産の継続的な拡大に伴い、大規模なウェーハ洗浄には自動洗浄システムが主流となっています。これらのシステムには、自動搬送機構、マルチタンク洗浄システム、そしてウェーハごとに一貫した洗浄結果を確保するための精密制御システムが搭載されていることが多くあります。
5. 今後の動向
半導体デバイスの微細化が進むにつれ、ウェーハ洗浄技術はより効率的で環境に優しいソリューションへと進化しています。将来の洗浄技術は、以下の点に重点を置くことになります。
サブナノメートル粒子の除去: 既存の洗浄技術はナノメートル規模の粒子を処理できますが、デバイスのサイズがさらに縮小すると、サブナノメートル粒子の除去が新たな課題になります。
グリーンで環境に優しい洗浄: 環境に有害な化学物質の使用を減らし、オゾン洗浄やメガソニック洗浄などのより環境に優しい洗浄方法を開発することがますます重要になります。
より高度な自動化とインテリジェンス: インテリジェント システムにより、洗浄プロセス中にさまざまなパラメータをリアルタイムで監視および調整できるようになり、洗浄の有効性と生産効率がさらに向上します。
半導体製造における重要な工程であるウェーハ洗浄技術は、後続工程におけるウェーハ表面の清浄性確保に極めて重要な役割を果たします。様々な洗浄方法を組み合わせることで、汚染物質を効果的に除去し、次工程に向けて清浄な基板表面を確保します。技術の進歩に伴い、洗浄プロセスは半導体製造における高精度化と不良率低減の要求に応えるべく、継続的に最適化されていきます。
投稿日時: 2024年10月8日