ウェーハダイシング技術は、半導体製造プロセスの重要なステップであり、チップのパフォーマンス、歩留まり、および製造コストに直接関係しています。
#01 ウェーハダイシングの背景と意義
1.1 ウェーハダイシングの定義
ウェーハダイシング(スクライビングとも呼ばれる)は、半導体製造において不可欠な工程であり、加工済みのウェーハを複数のダイに分割することを目的としています。これらのダイは通常、完全な回路機能を備えており、最終的に電子機器の製造に使用されるコア部品となります。チップ設計が複雑化し、寸法が縮小し続けるにつれて、ウェーハダイシング技術に対する精度と効率の要件はますます厳しくなっています。
実際の工程では、ウェーハダイシングでは通常、ダイヤモンドブレードなどの高精度工具を用いて、各ダイが損傷を受けず完全に機能することを保証しています。重要な手順としては、切断前の準備、切断工程中の精密な制御、そして切断後の品質検査が挙げられます。
切断前には、正確な切断経路を確保するために、ウェハにマーキングと位置決めを行う必要があります。切断中は、ウェハへの損傷を防ぐため、ツールの圧力や速度などのパラメータを厳密に制御する必要があります。切断後は、すべてのチップが性能基準を満たしていることを確認するために、包括的な品質検査を実施します。
ウェーハダイシング技術の基本原理は、切断装置の選択やプロセスパラメータの設定だけでなく、材料の機械的特性や特性が切断品質に与える影響も網羅しています。例えば、低誘電率(Low-k)誘電体シリコンウェーハは、機械的特性が劣るため、切断中に応力集中の影響を受けやすく、チッピングやクラックなどの不具合につながります。低誘電率材料は硬度が低く脆いため、特に切断中に機械的力や熱応力によって構造的な損傷を受けやすくなります。工具とウェーハ表面の接触と高温が相まって、応力集中はさらに悪化する可能性があります。
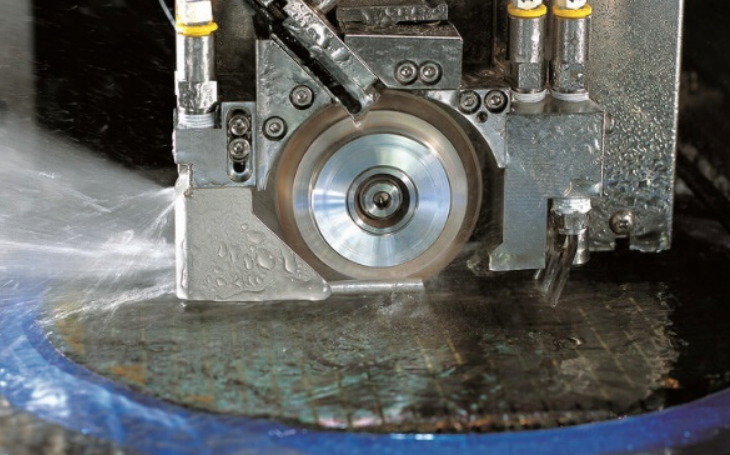
材料科学の進歩に伴い、ウェーハダイシング技術は従来のシリコンベースの半導体から、窒化ガリウム(GaN)などの新材料へと拡大しています。これらの新材料は、その硬度と構造特性により、ダイシングプロセスに新たな課題をもたらし、切削工具と技術のさらなる改良が求められています。
半導体業界の重要なプロセスであるウェーハダイシングは、進化する需要と技術の進歩に応じて最適化され続け、将来のマイクロエレクトロニクスと集積回路技術の基礎を築きます。
ウェーハダイシング技術の進歩は、補助材料やツールの開発にとどまりません。プロセスの最適化、装置の性能向上、そしてダイシングパラメータの精密制御もその範囲に含まれます。これらの進歩は、ウェーハダイシングプロセスにおける高精度、高効率、そして安定性の確保を目指しており、半導体業界の小型化、高集積化、そしてより複雑なチップ構造へのニーズに応えています。
改善エリア | 具体的な対策 | 効果 |
プロセス最適化 | - より正確なウェハの位置決めや経路計画などの初期準備を改善します。 | - 切断エラーを減らし、安定性を向上します。 |
- 切断エラーを最小限に抑え、安定性を高めます。 | - リアルタイムの監視およびフィードバック メカニズムを採用して、ツールの圧力、速度、温度を調整します。 | |
- ウェーハ破損率を下げ、チップ品質を向上させます。 | ||
機器性能向上 | - 高精度の機械システムと高度な自動化制御技術を活用します。 | - 切断精度を高め、材料の無駄を削減します。 |
・高硬度材料ウエハに適したレーザー切断技術を導入。 | - 生産効率を向上し、手作業によるエラーを削減します。 | |
- 自動監視および調整のために機器の自動化を強化します。 | ||
正確なパラメータ制御 | - 切削深さ、速度、ツールの種類、冷却方法などのパラメータを細かく調整します。 | - ダイの完全性と電気性能を確保します。 |
- ウェーハの材質、厚さ、構造に基づいてパラメータをカスタマイズします。 | - 歩留まり率を高め、材料の無駄を減らし、生産コストを削減します。 | |
戦略的意義 | - 市場の需要を満たすために、継続的に新しい技術的道筋を模索し、プロセスを最適化し、設備の機能を強化します。 | - チップ製造の歩留まりとパフォーマンスを向上させ、新しい材料と高度なチップ設計の開発をサポートします。 |
1.2 ウェーハダイシングの重要性
ウェーハダイシングは半導体製造プロセスにおいて極めて重要な役割を果たし、後続工程だけでなく最終製品の品質と性能にも直接影響を及ぼします。その重要性は以下のように詳述されます。
まず、ダイシングの精度と一貫性は、チップの歩留まりと信頼性を確保する上で重要です。製造工程では、ウェハは複数の処理工程を経て多数の複雑な回路構造を形成し、個々のチップ(ダイ)へと正確に分割する必要があります。ダイシング工程でアライメントや切断に大きな誤差が生じると、回路が損傷し、チップの機能と信頼性に影響を与える可能性があります。そのため、高精度ダイシング技術は、各チップの完全性を保証するだけでなく、内部回路の損傷を防ぎ、全体的な歩留まりを向上させます。
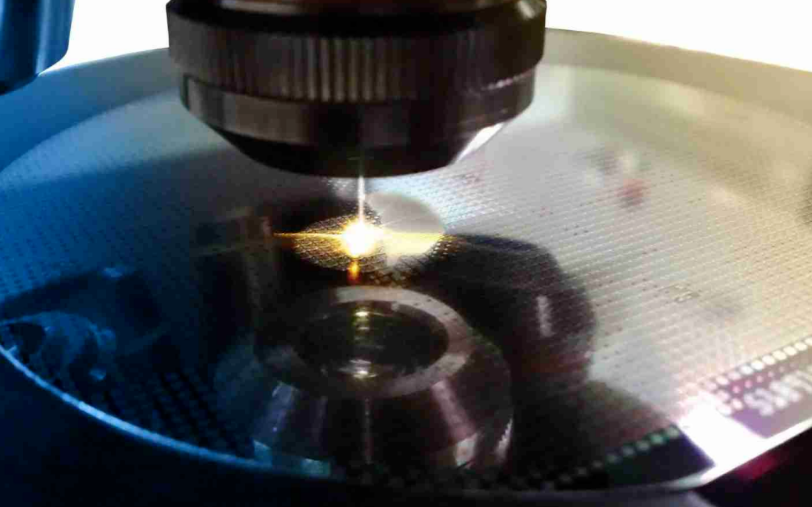
第二に、ウェーハダイシングは生産効率とコスト管理に大きな影響を与えます。製造プロセスにおける重要なステップであるダイシングの効率は、後続工程の進捗に直接影響します。ダイシング工程の最適化、自動化レベルの向上、切断速度の向上により、全体的な生産効率を大幅に向上させることができます。
一方、ダイシング時の材料ロスはコスト管理において重要な要素です。高度なダイシング技術を活用することで、切断工程における不要な材料ロスを削減できるだけでなく、ウェーハの利用率を高め、生産コストを削減できます。
半導体技術の進歩に伴い、ウェーハの直径は拡大し続け、回路密度もそれに応じて高まり、ダイシング技術への要求はますます高まっています。ウェーハの大型化に伴い、特に高密度回路領域では、切断パスのより精密な制御が求められます。わずかなずれでも複数のチップに不良品が発生する可能性があるためです。さらに、ウェーハの大型化に伴い、切断ラインの数が増え、工程も複雑化するため、これらの課題に対応するには、ダイシング技術の精度、一貫性、効率性をさらに向上させる必要があります。
1.3 ウェーハダイシングプロセス
ウェーハダイシングプロセスは、準備段階から最終品質検査まですべてのステップを網羅しており、各段階はダイシングされたチップの品質と性能を保証する上で非常に重要です。以下では、各段階について詳しく説明します。
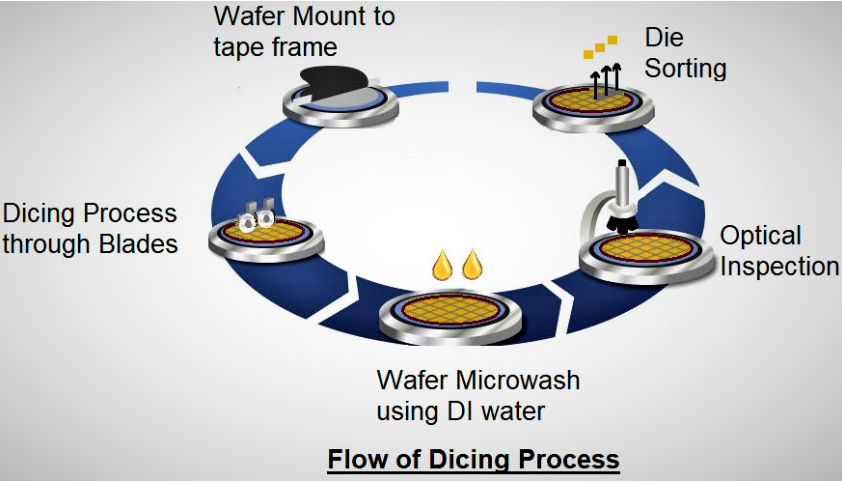
段階 | 詳細な説明 |
準備段階 | -ウェーハ洗浄: 高純度水と特殊な洗浄剤を超音波または機械洗浄と組み合わせて使用し、不純物、粒子、汚染物質を除去してきれいな表面を保ちます。 -正確な位置決め: 高精度の機器を使用して、設計された切断経路に沿ってウェハが正確に分割されるようにします。 -ウェーハ固定: 切断中の安定性を維持し、振動や動きによる損傷を防ぐために、ウェーハをテープ フレームに固定します。 |
切断段階 | -ブレードダイシング: 物理的な切断に高速回転ダイヤモンドコーティングブレードを採用しており、シリコンベースの材料に適しており、コスト効率に優れています。 -レーザーダイシング: 高エネルギーレーザービームを使用した非接触切断。窒化ガリウムなどの脆性または高硬度の材料に最適で、より高い精度とより少ない材料損失を実現します。 -新しいテクノロジーレーザー切断技術とプラズマ切断技術を導入し、熱影響部を最小限に抑えながら効率と精度をさらに向上させます。 |
洗浄段階 | - 脱イオン水 (DI 水) と特殊な洗浄剤を超音波洗浄またはスプレー洗浄と組み合わせて使用し、切断中に発生した破片やほこりを除去して、残留物が後続のプロセスやチップの電気的性能に影響を与えないようにします。 - 高純度の DI 水は新たな汚染物質の導入を防ぎ、クリーンなウェーハ環境を確保します。 |
検査フェーズ | -光学検査: AI アルゴリズムと組み合わせた光学検出システムを使用して欠陥を迅速に特定し、ダイシングされたチップにひび割れや欠けがないことを確認し、検査効率を向上させ、人的エラーを削減します。 -寸法測定: チップの寸法が設計仕様を満たしていることを確認します。 -電気性能試験: 重要なチップの電気的性能が基準を満たしていることを確認し、後続のアプリケーションにおける信頼性を保証します。 |
分類フェーズ | - ロボットアームまたは真空吸引カップを使用して、適格なチップをテープフレームから分離し、パフォーマンスに基づいて自動的に分類することで、生産効率と柔軟性を確保しながら精度を向上させます。 |
ウェーハ切断工程には、ウェーハの洗浄、位置決め、切断、洗浄、検査、選別といった工程が含まれており、それぞれの工程が極めて重要です。自動化、レーザー切断、AI検査技術の進歩により、現代のウェーハ切断システムは、より高い精度、より高い速度、そしてより低い材料ロスを実現しています。将来的には、レーザーやプラズマといった新しい切断技術が、ますます複雑化するチップ設計のニーズに応えるため、従来のブレード切断に徐々に取って代わり、半導体製造プロセスの発展をさらに推進していくでしょう。
ウェーハ切断技術とその原理
この画像は、3 つの一般的なウェーハ切断技術を示しています。ブレードダイシング、レーザーダイシング、 そしてプラズマダイシング以下では、これら3つの手法の詳細な分析と補足説明を示します。
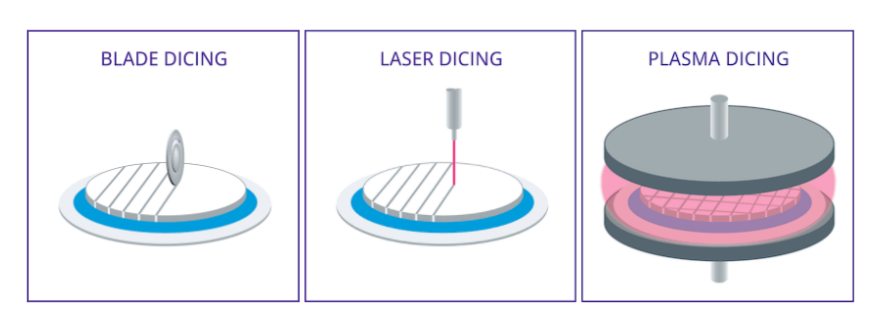
半導体製造において、ウェーハ切断は重要な工程であり、ウェーハの厚さに応じて適切な切断方法を選択する必要があります。まず、ウェーハの厚さを決定します。ウェーハの厚さが100ミクロンを超える場合は、切断方法としてブレードダイシングを選択できます。ブレードダイシングが適さない場合は、スクライブカットとブレードダイシングの両方の技術を含むフラクチャーダイシング法を使用できます。
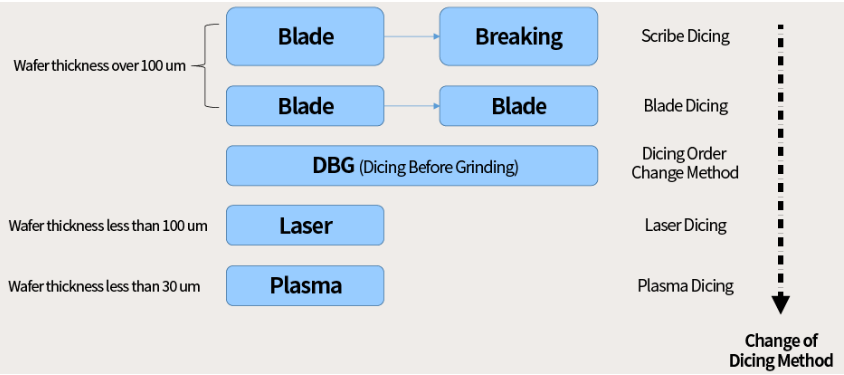
ウェーハの厚さが30~100ミクロンの場合、DBG(Dice Before Grinding)方式が推奨されます。この場合、スクライブカット、ブレードダイシング、または必要に応じてカットシーケンスを調整することで、最良の結果を得ることができます。
厚さ30ミクロン未満の極薄ウェハの場合、レーザー切断は過度の損傷を与えることなく薄いウェハを正確に切断できるため、好ましい方法となります。レーザー切断では特定の要件を満たせない場合は、プラズマ切断を代替手段として使用できます。このフローチャートは、様々な厚さの条件において最適なウェハ切断技術を選択するための明確な意思決定パスを提供します。
2.1 機械切断技術
機械切断技術は、ウェーハダイシングにおける伝統的な方法です。その基本原理は、高速回転するダイヤモンド砥石を切削工具として用いてウェーハをスライスすることです。主要な装置には、ダイヤモンド砥石工具を高速で駆動し、所定の切削パスに沿って精密な切断または溝入れ加工を行うエアベアリングスピンドルが含まれます。この技術は、低コスト、高効率、そして幅広い適用性から、業界で広く使用されています。
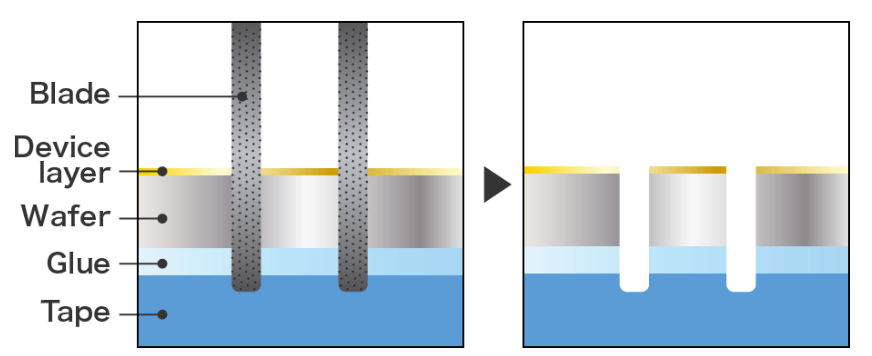
利点
ダイヤモンド砥石工具の高い硬度と耐摩耗性により、機械切断技術は、従来のシリコンベースの材料から最新の化合物半導体まで、様々なウェーハ材料の切断ニーズに適応することができます。操作はシンプルで、技術的要件も比較的低いため、大量生産における普及がさらに進んでいます。さらに、レーザー切断などの他の切断方法と比較して、機械切断はコスト管理が容易であるため、大量生産のニーズに適しています。
制限事項
機械切断技術は多くの利点がある一方で、限界もあります。まず、工具とウェハが物理的に接触するため、切断精度は比較的限られており、寸法偏差が生じやすく、後続のチップパッケージングやテストの精度に影響を与える可能性があります。次に、機械切断工程では欠けやひび割れなどの欠陥が発生しやすく、歩留まりに影響を与えるだけでなく、チップの信頼性と寿命にも悪影響を与える可能性があります。機械的な応力によって引き起こされる損傷は、高密度チップの製造において特に有害であり、特に脆性材料の切断においては、これらの問題がより顕著になります。
技術の進歩
これらの限界を克服するため、研究者たちは機械的な切断プロセスの最適化に継続的に取り組んでいます。主な改善点としては、研削ホイールの設計と材料選定の強化により、切断精度と耐久性を向上させることが挙げられます。さらに、切断装置の構造設計と制御システムの最適化により、切断プロセスの安定性と自動化がさらに向上しました。これらの進歩により、人為的な操作によるエラーが低減し、切断の一貫性が向上しました。さらに、切断プロセス中の異常をリアルタイムで監視する高度な検査・品質管理技術の導入により、切断の信頼性と歩留まりも大幅に向上しました。
将来の開発と新技術
機械切断技術は依然としてウェーハ切断において重要な位置を占めていますが、半導体プロセスの進化に伴い、新たな切断技術が急速に進歩しています。例えば、熱レーザー切断技術の応用は、機械切断における精度と欠陥の問題に対する新たな解決策を提供します。この非接触切断方法は、ウェーハへの物理的ストレスを軽減し、特に脆性材料の切断において、チッピングやクラックの発生率を大幅に低減します。将来的には、機械切断技術と新興の切断技術を統合することで、半導体製造の選択肢と柔軟性が広がり、製造効率とチップ品質がさらに向上するでしょう。
結論として、機械切断技術には一定の欠点があるものの、継続的な技術改善と新しい切断技術との統合により、依然として半導体製造において重要な役割を果たし、将来のプロセスにおいても競争力を維持することができます。
2.2 レーザー切断技術
レーザー切断技術は、ウェーハ切断における新たな手法として、その高精度、機械的な接触損傷の少なさ、そして迅速な切断能力により、半導体業界で徐々に注目を集めています。この技術は、レーザービームの高いエネルギー密度と集光性を利用して、ウェーハ材料の表面に小さな熱影響部を形成します。レーザービームをウェーハに照射すると、発生する熱応力によって材料が所定の位置で破断し、精密な切断を実現します。
レーザー切断技術の利点
• 高精度: レーザー ビームの正確な位置決め機能により、ミクロン、さらにはナノメートル レベルの切断精度が可能になり、現代の高精度、高密度の集積回路製造の要件を満たします。
• 機械的な接触なしレーザー切断はウェハとの物理的な接触を回避するため、欠けや割れなど機械切断でよく見られる問題を防ぎ、チップの歩留まりと信頼性を大幅に向上させます。
• 高速切断速度: レーザー切断の高速性は生産効率の向上に貢献し、特に大規模で高速な生産シナリオに適しています。
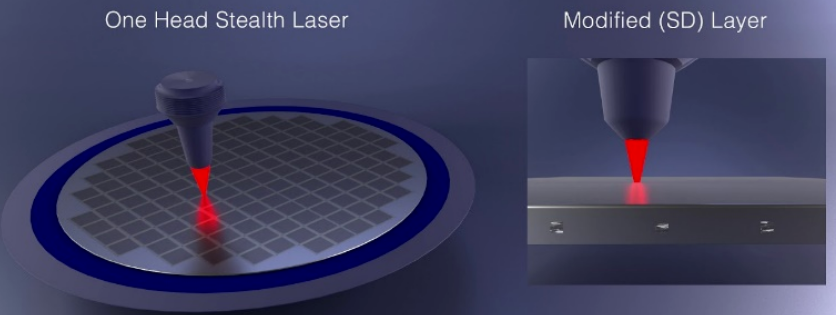
直面した課題
• 設備コストが高いレーザー切断装置への初期投資は高額であり、特に中小規模の製造企業にとっては経済的な圧力となります。
• 複雑なプロセス制御レーザー切断では、エネルギー密度、焦点位置、切断速度など、いくつかのパラメータを正確に制御する必要があり、プロセスが複雑になります。
• 熱影響部の問題レーザー切断は非接触であるため機械的損傷は軽減されますが、熱影響部(HAZ)によって生じる熱応力はウェハ材料の特性に悪影響を及ぼす可能性があります。この影響を最小限に抑えるには、プロセスのさらなる最適化が必要です。
技術改善の方向性
これらの課題に対処するために、研究者は設備コストの削減、切断効率の向上、プロセスフローの最適化に重点を置いています。
• 効率的なレーザーと光学システム: より効率的なレーザーと高度な光学システムを開発することで、切断精度と速度を向上させながら設備コストを削減することが可能です。
• プロセスパラメータの最適化レーザーとウェーハ材料の相互作用に関する詳細な研究が行われており、熱影響部を減らすプロセスを改善して切断品質を向上させています。
• インテリジェント制御システムインテリジェント制御技術の開発は、レーザー切断プロセスを自動化および最適化し、その安定性と一貫性を向上させることを目的としています。
レーザー切断技術は、超薄型ウェーハや高精度切断において特に効果的です。ウェーハサイズの大型化と回路密度の向上に伴い、従来の機械式切断方法では、現代の半導体製造における高精度・高効率の要求を満たすことが困難になっています。レーザー切断は、その独自の利点により、これらの分野において最適なソリューションになりつつあります。
レーザー切断技術は、依然として設備コストの高さやプロセスの複雑さといった課題に直面していますが、高精度と非接触切断という独自の利点により、半導体製造における重要な発展方向となっています。レーザー技術とインテリジェント制御システムの進歩に伴い、レーザー切断はウェーハ切断の効率と品質をさらに向上させ、半導体産業の継続的な発展を牽引すると期待されています。
2.3 プラズマ切断技術
プラズマ切断技術は、近年、ウェーハダイシングの新たな手法として大きな注目を集めています。この技術は、高エネルギープラズマビームを用いてウェーハを精密に切断し、そのエネルギー、速度、切断経路を制御することで、最適な切断結果を実現します。
動作原理と利点
プラズマ切断プロセスは、装置によって生成される高温・高エネルギーのプラズマビームに依存しています。このビームは、ウェハ材料を非常に短時間で融点または気化点まで加熱するため、高速切断が可能になります。従来の機械切断やレーザー切断と比較して、プラズマ切断は高速で熱影響部が小さいため、切断中のひび割れや損傷の発生を効果的に低減します。
実用分野において、プラズマ切断技術は複雑な形状のウェハの取り扱いに特に優れています。高エネルギーで調整可能なプラズマビームは、不規則な形状のウェハを高精度かつ容易に切断できます。そのため、マイクロエレクトロニクス製造、特にハイエンドチップのカスタマイズ生産や小ロット生産において、この技術は広く普及することが期待されています。
課題と限界
プラズマ切断技術には多くの利点があるにもかかわらず、いくつかの課題も存在します。
• 複雑なプロセス: プラズマ切断プロセスは複雑であり、高精度の装置と経験豊富なオペレーターが必要です。切断の精度と安定性。
• 環境管理と安全プラズマビームは高温、高エネルギーの性質を持つため、厳格な環境制御と安全対策が必要となり、実装の複雑さとコストが増加します。
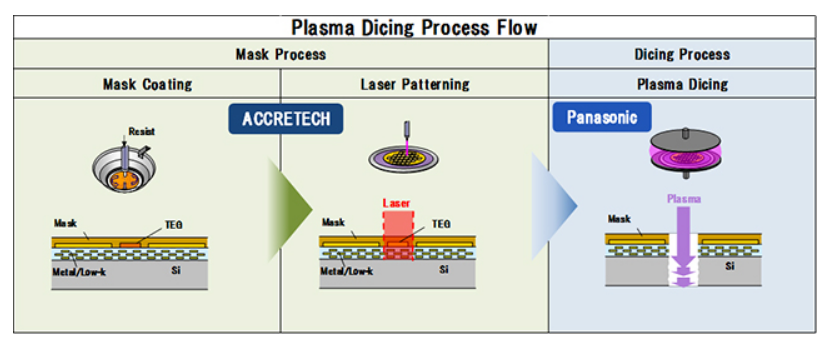
今後の開発方向
技術の進歩により、プラズマ切断に伴う課題は徐々に克服されると期待されています。よりスマートで安定した切断装置を開発することで、手作業への依存度を低減し、生産効率を向上させることができます。同時に、プロセスパラメータと切断環境を最適化することで、安全リスクと運用コストの低減にも貢献します。
半導体産業において、ウェーハ切断・ダイシング技術の革新は、業界の発展を牽引する上で極めて重要です。高精度、高効率、そして複雑なウェーハ形状への対応力を備えたプラズマ切断技術は、この分野における重要な新技術として台頭しています。依然として課題は残っていますが、継続的な技術革新によってこれらの課題は徐々に解決され、半導体製造にさらなる可能性と機会をもたらすでしょう。
プラズマ切断技術の応用展望は広大であり、将来的には半導体製造においてより重要な役割を果たすことが期待されています。継続的な技術革新と最適化を通じて、プラズマ切断は既存の課題を解決するだけでなく、半導体産業の成長を強力に推進する原動力となるでしょう。
2.4 切断品質と影響要因
ウェーハ切断品質は、その後のチップパッケージング、テスト、そして最終製品の全体的な性能と信頼性にとって非常に重要です。切断中に発生する一般的な問題には、ひび割れ、欠け、切断偏差などがあります。これらの問題は、複数の要因が相互に影響し合いながら発生します。
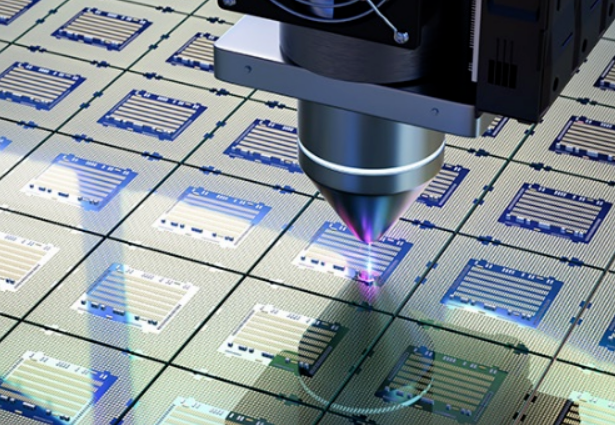
カテゴリ | コンテンツ | インパクト |
プロセスパラメータ | 切削速度、送り速度、切削深さは、切削プロセスの安定性と精度に直接影響します。不適切な設定は、応力集中や過度の熱影響部(HAZ)の発生につながり、ひび割れや欠けの原因となります。ウェーハの材質、厚さ、そして切削条件に基づいてパラメータを適切に調整することが、望ましい切削結果を得るための鍵となります。 | 適切なプロセスパラメータにより、正確な切断が保証され、ひび割れや欠けなどの欠陥のリスクが軽減されます。 |
設備と材料の要因 | -刃の品質刃の材質、硬度、耐摩耗性は、切断の滑らかさと切断面の平坦性に影響を与えます。品質の悪い刃は摩擦と熱応力を増加させ、ひび割れや欠けを引き起こす可能性があります。適切な刃の材質を選択することが重要です。 -冷却性能クーラントは切削温度を下げ、摩擦を最小限に抑え、切削屑を除去するのに役立ちます。効果のないクーラントは、切削温度の上昇や切削屑の蓄積につながり、切削品質と効率に悪影響を及ぼす可能性があります。効率的で環境に優しいクーラントを選択することが重要です。 | ブレードの品質は、切断の精度と滑らかさに影響を与えます。クーラントが効果的でないと、切断品質と効率が低下する可能性があるため、最適なクーラントの使用が不可欠です。 |
プロセス制御と品質検査 | -プロセス制御: 主要な切断パラメータをリアルタイムで監視および調整し、切断プロセスの安定性と一貫性を確保します。 -品質検査: 切断後の外観チェック、寸法測定、電気性能テストにより、品質の問題を迅速に特定して対処し、切断の精度と一貫性を向上させることができます。 | 適切なプロセス制御と品質検査により、一貫した高品質の切断結果が保証され、潜在的な問題が早期に検出されます。 |

切断品質の向上
切断品質の向上には、プロセスパラメータ、装置および材料の選定、プロセス制御、検査などを考慮した包括的なアプローチが必要です。切断技術を継続的に改良し、プロセス方法を最適化することで、ウェーハ切断の精度と安定性をさらに向上させ、半導体製造業界に信頼性の高い技術サポートを提供できます。
#03 切断後の取り扱いとテスト
3.1 洗浄と乾燥
ウェーハ切断後の洗浄と乾燥工程は、チップの品質を確保し、後続工程をスムーズに進めるために非常に重要です。この段階では、切断中に発生したシリコンデブリ、クーラント残留物、その他の汚染物質を徹底的に除去することが不可欠です。洗浄工程中にチップが損傷しないようにすることも同様に重要です。また、乾燥後には、腐食や静電放電などの問題を防ぐために、チップ表面に水分が残らないようにすることも重要です。
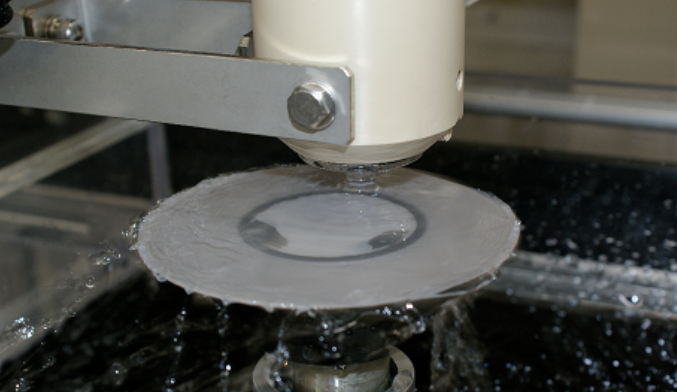
切断後の処理:洗浄と乾燥工程
プロセスステップ | コンテンツ | インパクト |
洗浄プロセス | -方法: 洗浄には専用の洗浄剤と純水を使用し、超音波または機械的なブラッシング技術を組み合わせて使用します。 | 汚染物質を徹底的に除去し、洗浄中にチップが損傷するのを防ぎます。 |
-洗浄剤の選択: チップを損傷することなく効果的な洗浄を確実に行うために、ウェーハの材質と汚染物質の種類に基づいて選択します。 | 適切な薬剤の選択が、効果的な洗浄とチップ保護の鍵となります。 | |
-パラメータ制御: 洗浄温度、時間、洗浄液濃度を厳密に管理し、不適切な洗浄による品質問題を防ぎます。 | 制御により、ウェハの損傷や汚染物質の残留を回避し、一貫した品質を確保できます。 | |
乾燥工程 | -伝統的な方法自然乾燥や温風乾燥は効率が低く、静電気が発生しやすくなります。 | 乾燥時間が遅くなり、静電気が問題になる可能性もあります。 |
-現代のテクノロジー: 真空乾燥や赤外線乾燥などの高度な技術を使用して、チップが素早く乾燥し、有害な影響が回避されるようにします。 | 乾燥プロセスがより速く、より効率的になり、静電気放電や湿気関連の問題のリスクが軽減されます。 | |
機器の選択とメンテナンス | -機器の選択高性能洗浄・乾燥機により処理効率が向上し、取り扱い時に発生する可能性のある問題を細かく制御します。 | 高品質の機械により、処理能力が向上し、洗浄と乾燥中にエラーが発生する可能性が低減します。 |
-機器メンテナンス: 機器の定期的な検査とメンテナンスにより、機器が最適な動作状態に維持され、チップの品質が保証されます。 | 適切なメンテナンスにより機器の故障を防ぎ、信頼性が高く高品質な処理を保証します。 |
切断後の洗浄と乾燥
ウェハ切断後の洗浄と乾燥工程は複雑かつ繊細なプロセスであり、最終的な処理結果を確実にするためには、複数の要素を慎重に検討する必要があります。科学的な手法と厳格な手順を用いることで、各チップが最適な状態で後続のパッケージングおよびテスト工程に進むことが可能になります。
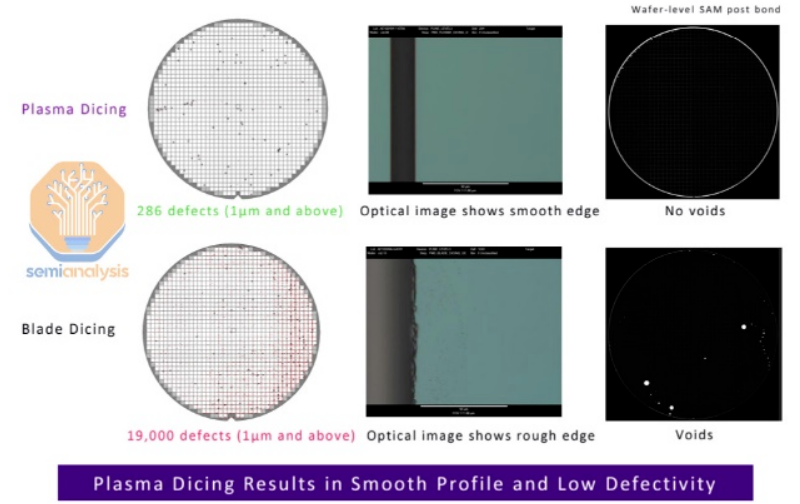
切断後の検査と試験
ステップ | コンテンツ | インパクト |
検査ステップ | 1.目視検査目視検査装置または自動検査装置を用いて、チップ表面のひび割れ、欠け、汚染などの目に見える欠陥を検査します。物理的に損傷したチップを迅速に特定し、廃棄を回避します。 | プロセスの早い段階で不良チップを特定して除去し、材料の損失を削減するのに役立ちます。 |
2.サイズ測定: 精密測定装置を使用してチップの寸法を正確に測定し、カット サイズが設計仕様を満たしていることを確認し、パフォーマンスの問題やパッケージングの困難を防止します。 | チップが必要なサイズ制限内に収まっていることを確認し、パフォーマンスの低下や組み立て上の問題を防ぎます。 | |
3.電気性能試験: 抵抗、静電容量、インダクタンスなどの主要な電気パラメータを評価して、非準拠のチップを識別し、パフォーマンスが認定されたチップだけが次の段階に進むようにします。 | 機能とパフォーマンスがテストされたチップのみがプロセスに進められるようにし、後の段階で障害が発生するリスクを軽減します。 | |
テストステップ | 1.機能テスト: チップの基本機能が意図したとおりに動作することを確認し、機能異常のあるチップを特定して排除します。 | 後の段階に進む前に、チップが基本的な動作要件を満たしていることを確認します。 |
2.信頼性試験: 長期間の使用や過酷な環境下でのチップのパフォーマンスの安定性を評価します。通常、高温老化、低温テスト、湿度テストなどにより、実際の過酷な条件をシミュレートします。 | さまざまな環境条件下でチップが確実に機能することを保証し、製品の寿命と安定性を向上させます。 | |
3.互換性テスト: チップが他のコンポーネントまたはシステムと正常に動作することを確認し、非互換性による障害やパフォーマンスの低下がないことを確認します。 | 互換性の問題を防ぐことで、実際のアプリケーションでのスムーズな操作を保証します。 |
3.3 包装と保管
ウェハ切断後のチップは半導体製造プロセスの重要な出力であり、その包装と保管段階も同様に重要です。適切な包装と保管対策は、輸送・保管中のチップの安全性と安定性を確保するだけでなく、その後の製造、試験、包装段階を強力にサポートするためにも不可欠です。
検査およびテスト段階の概要:
ウェハ切断後のチップの検査・試験工程は、外観検査、寸法測定、電気性能試験、機能試験、信頼性試験、適合性試験など、多岐にわたります。これらの工程は相互に連携し、相互に補完し合うことで、製品の品質と信頼性を確保するための強固な障壁を形成します。厳格な検査・試験手順により、潜在的な問題を特定し、迅速に解決することで、最終製品がお客様の要件と期待を満たすことを保証します。
側面 | コンテンツ |
梱包対策 | 1.静電気防止: 静電気によるデバイスの損傷や性能への影響を防ぐために、梱包材には優れた帯電防止特性が必要です。 |
2.防湿: 湿度による腐食や電気性能の低下を防ぐために、梱包材は耐湿性に優れていなければなりません。 | |
3.耐衝撃性: 輸送中の振動や衝撃からチップを保護するために、梱包材は効果的な衝撃吸収性を備えている必要があります。 | |
保管環境 | 1.湿度制御: 湿度を適正範囲内に厳密に管理し、湿度過度による吸湿・腐食や湿度低さによる静電気問題を防ぎます。 |
2.清潔さ: チップがほこりや不純物で汚染されないように、清潔な保管環境を維持します。 | |
3.温度制御: 過度の熱による老化の加速や低温による結露の問題を防ぐために、適切な温度範囲を設定し、温度の安定性を維持します。 | |
定期検査 | 保管中のチップは、目視検査、サイズ測定、電気性能試験などを用いて定期的に点検・評価し、潜在的な問題を適時に特定・対処します。保管期間と保管状況に基づき、チップの使用計画を立て、最適な状態で使用するようにしてください。 |
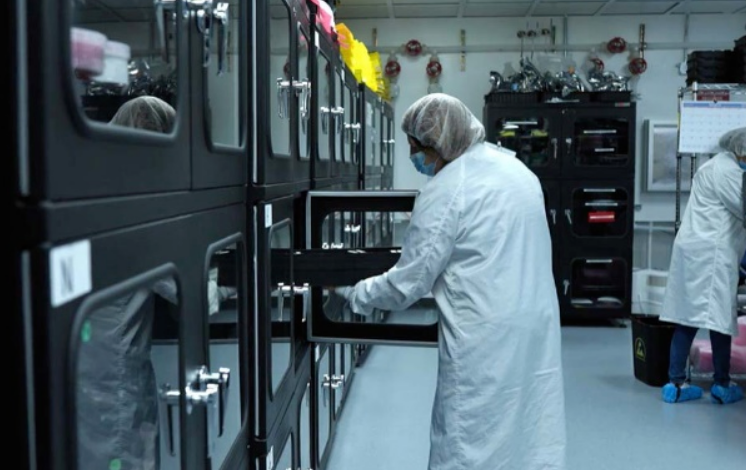
ウェーハダイシング工程におけるマイクロクラックや損傷の問題は、半導体製造における大きな課題です。この現象の主な原因は切断応力であり、ウェーハ表面に微細なクラックや損傷が生じ、製造コストの増加と製品品質の低下につながります。
この課題に対処するには、切削応力を最小限に抑え、最適化された切削技術、工具、および条件を導入することが不可欠です。ブレード材質、切削速度、圧力、冷却方法といった要素に細心の注意を払うことで、マイクロクラックの発生を低減し、プロセス全体の歩留まりを向上させることができます。さらに、レーザーダイシングなどのより高度な切削技術の継続的な研究により、これらの問題をさらに軽減する方法が模索されています。
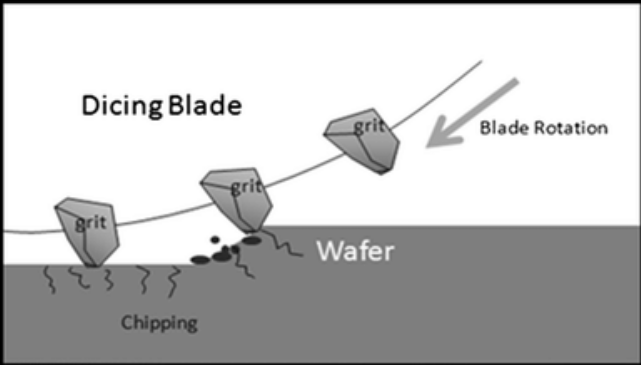
脆い材料であるウェーハは、機械的、熱的、または化学的ストレスを受けると内部構造が変化しやすく、マイクロクラック(微小亀裂)の形成につながります。これらの亀裂はすぐには目立たない場合もありますが、製造プロセスが進むにつれて拡大し、より深刻な損傷を引き起こす可能性があります。この問題は、その後のパッケージングおよびテスト段階で特に深刻化します。温度変動や追加の機械的ストレスによって、これらのマイクロクラックが目に見える亀裂へと発展し、チップの故障につながる可能性があります。
このリスクを軽減するには、切断速度、圧力、温度などのパラメータを最適化し、切断プロセスを綿密に制御することが不可欠です。レーザーダイシングなど、より低負荷の切断方法を用いることで、ウェーハへの機械的ストレスを軽減し、マイクロクラックの発生を最小限に抑えることができます。さらに、ウェーハダイシング工程中に赤外線スキャンやX線イメージングなどの高度な検査方法を導入することで、クラックがさらなる損傷を引き起こす前に、早期段階で検出することが可能になります。
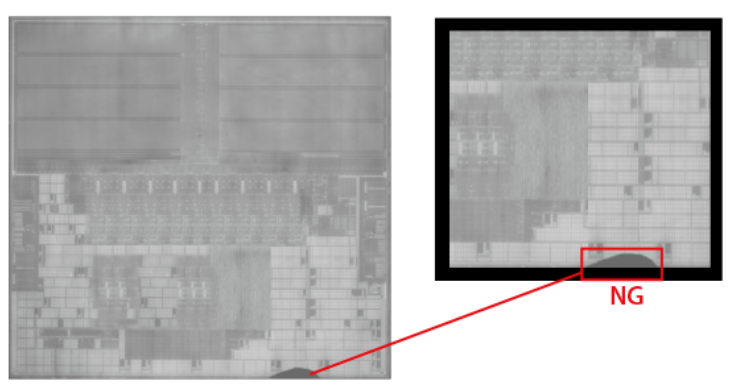
ダイシング工程において、ウェーハ表面の損傷はチップの性能と信頼性に直接影響を与える可能性があるため、重大な懸念事項です。このような損傷は、切削工具の不適切な使用、不適切な切削パラメータ、あるいはウェーハ自体に内在する材料欠陥などによって引き起こされる可能性があります。原因に関わらず、これらの損傷は回路の電気抵抗や静電容量の変化につながり、全体的な性能に影響を及ぼす可能性があります。
これらの問題に対処するために、次の 2 つの主要な戦略が検討されています。
1.切削工具とパラメータの最適化: より鋭い刃を使用し、切断速度を調整し、切断深さを変更することで、切断プロセス中の応力集中を最小限に抑え、損傷の可能性を減らすことができます。
2.新しい切削技術の探求レーザー切断やプラズマ切断といった高度な技術は、精度を向上させると同時に、ウェハへのダメージを低減する可能性を秘めています。これらの技術は、ウェハへの熱的・機械的ストレスを最小限に抑えながら、高い切断精度を実現する方法を見つけるために研究されています。
熱影響部と性能への影響
レーザー切断やプラズマ切断などの熱切断プロセスでは、高温によりウェハ表面に熱影響部が必然的に形成されます。この領域では温度勾配が顕著になり、材料特性が変化し、チップの最終的な性能に影響を与える可能性があります。
熱影響部(TAZ)の影響:
結晶構造の変化高温下では、ウェーハ材料内の原子が再配列し、結晶構造に歪みが生じる可能性があります。この歪みにより材料が弱体化し、機械的強度と安定性が低下し、使用中にチップが故障するリスクが高まります。
電気特性の変化高温は半導体材料のキャリア濃度と移動度を変化させ、チップの電気伝導性と電流伝送効率に影響を与える可能性があります。これらの変化はチップの性能低下につながり、本来の用途に適さなくなる可能性があります。
これらの影響を軽減するには、切断中の温度を制御し、切断パラメータを最適化し、冷却ジェットや後処理などの方法を検討することが、熱の影響の範囲を減らして材料の完全性を維持するための重要な戦略です。
全体として、マイクロクラックと熱衝撃領域は、ウェーハダイシング技術における重要な課題です。半導体製品の品質を向上させ、市場競争力を強化するためには、技術の進歩と品質管理対策に加え、継続的な研究が不可欠です。
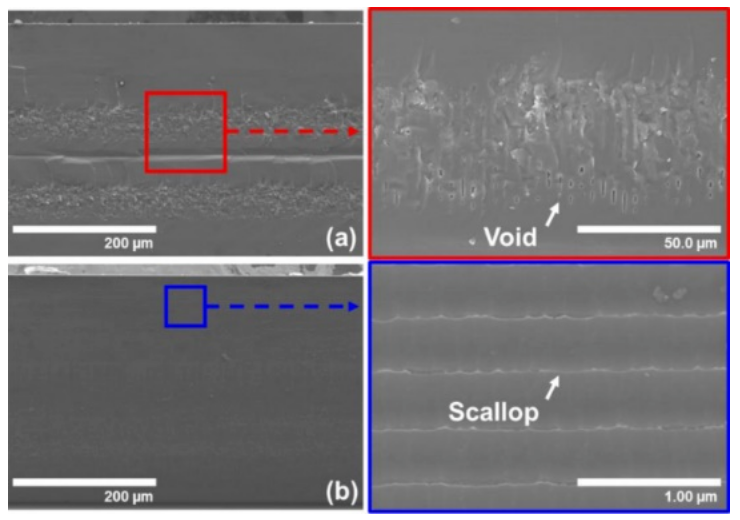
熱影響部の制御対策:
切断プロセスパラメータの最適化切断速度と出力を低減することで、熱影響部(TAZ)の大きさを効果的に最小化できます。これにより、切断プロセス中に発生する熱量を制御し、ウェーハの材料特性に直接影響を与えることができます。
高度な冷却技術液体窒素冷却やマイクロ流体冷却などの技術を適用することで、熱影響領域の範囲を大幅に制限できます。これらの冷却方法は、熱をより効率的に放散させ、ウェハの材料特性を維持し、熱による損傷を最小限に抑えるのに役立ちます。
材料の選択研究者たちは、優れた熱伝導性と機械的強度を備えたカーボンナノチューブやグラフェンといった新素材の研究に取り組んでいます。これらの材料は、熱影響部を縮小すると同時に、チップ全体の性能を向上させることができます。
まとめると、熱影響部は熱切断技術の必然的な結果ではあるものの、加工技術と材料の選択を最適化することで効果的に制御することが可能です。今後の研究では、より効率的で高精度なウェーハダイシングを実現するために、熱切断プロセスの微調整と自動化に焦点が当てられるでしょう。

バランス戦略:
ウェーハダイシング技術において、ウェーハの歩留まりと生産効率の最適なバランスを実現することは、常に課題となっています。メーカーは、市場需要、生産コスト、製品品質など、複数の要素を考慮し、合理的な生産戦略とプロセスパラメータを策定する必要があります。同時に、高度な切断装置の導入、オペレーターのスキル向上、原材料の品質管理の強化は、生産効率を高めながら歩留まりを維持、あるいは向上させるために不可欠です。
将来の課題と機会:
半導体技術の進歩に伴い、ウェーハ切断は新たな課題と機会に直面しています。チップサイズの縮小と集積度の向上に伴い、切断精度と品質に対する要求は著しく高まっています。同時に、新興技術はウェーハ切断技術の開発に新たなアイデアをもたらします。メーカーは市場の動向と技術動向を常に把握し、市場の変化と技術要求に対応するために、生産戦略とプロセスパラメータを継続的に調整・最適化する必要があります。
結論として、市場の需要、生産コスト、製品品質を総合的に考慮し、先進的な設備と技術を導入し、作業者のスキルを向上させ、原材料管理を強化することで、メーカーはウェーハダイシング時のウェーハ歩留まりと生産効率の最適なバランスを実現し、効率的で高品質な半導体製品の生産を実現することができます。
今後の展望:
急速な技術進歩に伴い、半導体技術はかつてないスピードで進歩しています。半導体製造における重要なステップであるウェーハ切断技術は、画期的な新技術開発の時を迎えています。今後、ウェーハ切断技術は精度、効率、コストの大幅な向上を実現し、半導体産業の継続的な成長に新たな活力をもたらすことが期待されています。
精度の向上:
より高い精度を追求する中で、ウェーハ切断技術は既存プロセスの限界を絶えず押し広げていきます。切断プロセスの物理的・化学的メカニズムを深く研究し、切断パラメータを精密に制御することで、より微細な切断結果が得られ、ますます複雑化する回路設計要件を満たすことができます。さらに、新しい材料や切断方法の探求により、歩留まりと品質が大幅に向上します。
効率性の向上:
新しいウェーハ切断装置は、スマートで自動化された設計に重点を置きます。高度な制御システムとアルゴリズムの導入により、装置は様々な材料や設計要件に合わせて切断パラメータを自動調整できるようになり、生産効率を大幅に向上させます。マルチウェーハ切断技術や高速ブレード交換システムなどの革新は、効率向上に重要な役割を果たすでしょう。
コスト削減:
コスト削減は、ウェーハ切断技術開発における重要な方向性です。新しい材料や切断方法が開発されるにつれて、設備コストとメンテナンス費用を効果的に抑制できるようになることが期待されます。さらに、生産プロセスの最適化とスクラップ率の低減により、製造中の廃棄物がさらに削減され、全体的な生産コストの削減につながります。
スマート製造とIoT:
スマートマニュファクチャリングとモノのインターネット(IoT)技術の統合は、ウェーハ切断技術に革新的な変化をもたらします。デバイス間の相互接続とデータ共有により、生産プロセスのあらゆるステップをリアルタイムで監視・最適化できるようになります。これにより、生産効率と製品品質が向上するだけでなく、企業はより正確な市場予測と意思決定支援を受けることができます。
今後、ウェーハ切断技術は精度、効率、コストの面で飛躍的な進歩を遂げるでしょう。これらの進歩は半導体産業の継続的な発展を牽引し、人類社会にさらなる技術革新と利便性をもたらすでしょう。
投稿日時: 2024年11月19日